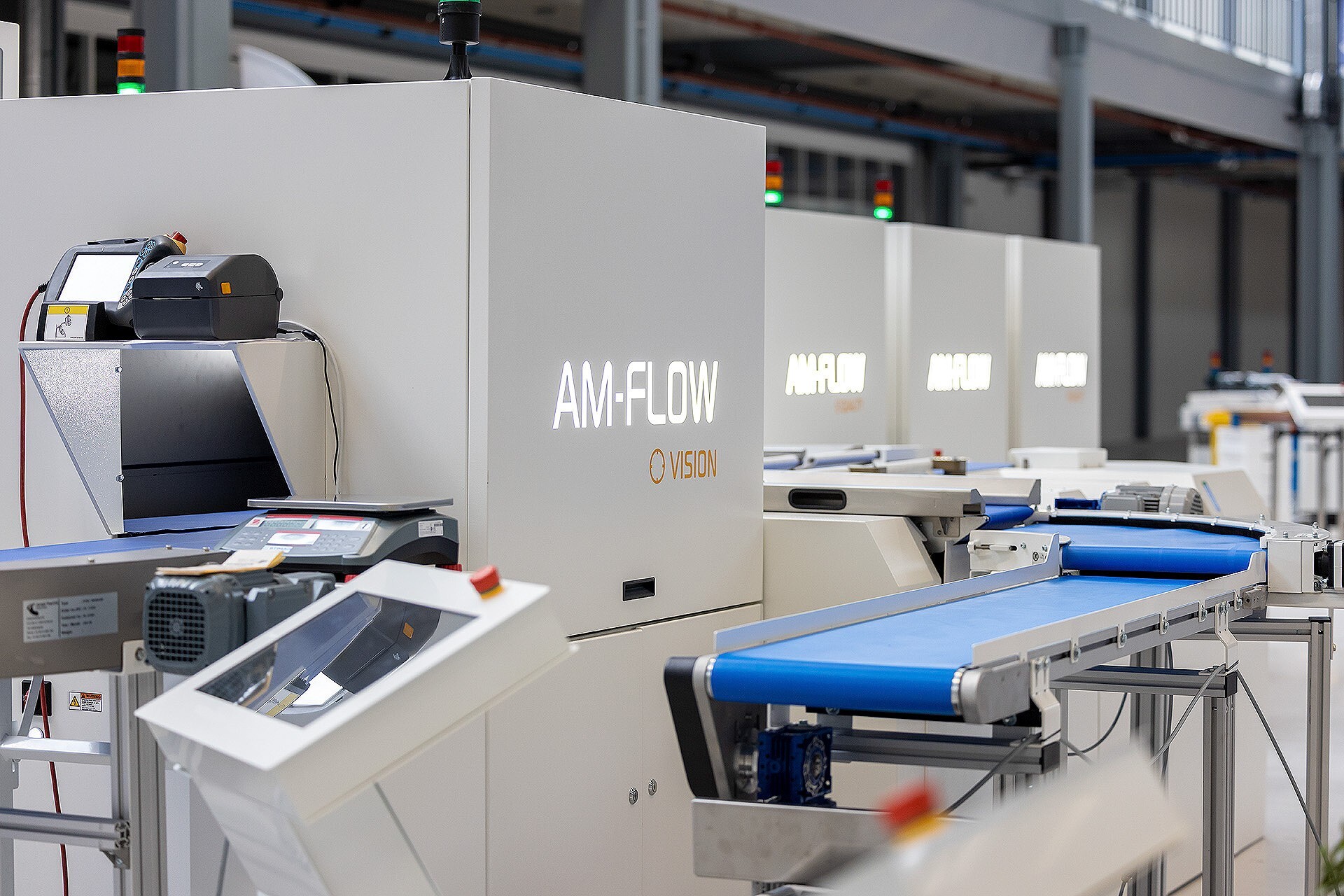
Perfektion ohne Kompromisse
Automatisiertes Bauteil-Matching neu definiert
Fallstudie: Vollautomatisches Matching von individuellen Bauteilen ohne Anlernen
Projektbeschreibung
Dieses Projekt befasst sich mit einem System, das vollautomatisch individuelle Bauteile (Unikate) erkennt und zuordnet. Das Ziel ist ein sekundenschnelles Abgleichen der Bauteile mit virtuellen STL-Daten und das Ermitteln sowie Dokumentieren von Soll-Ist-Differenzen.
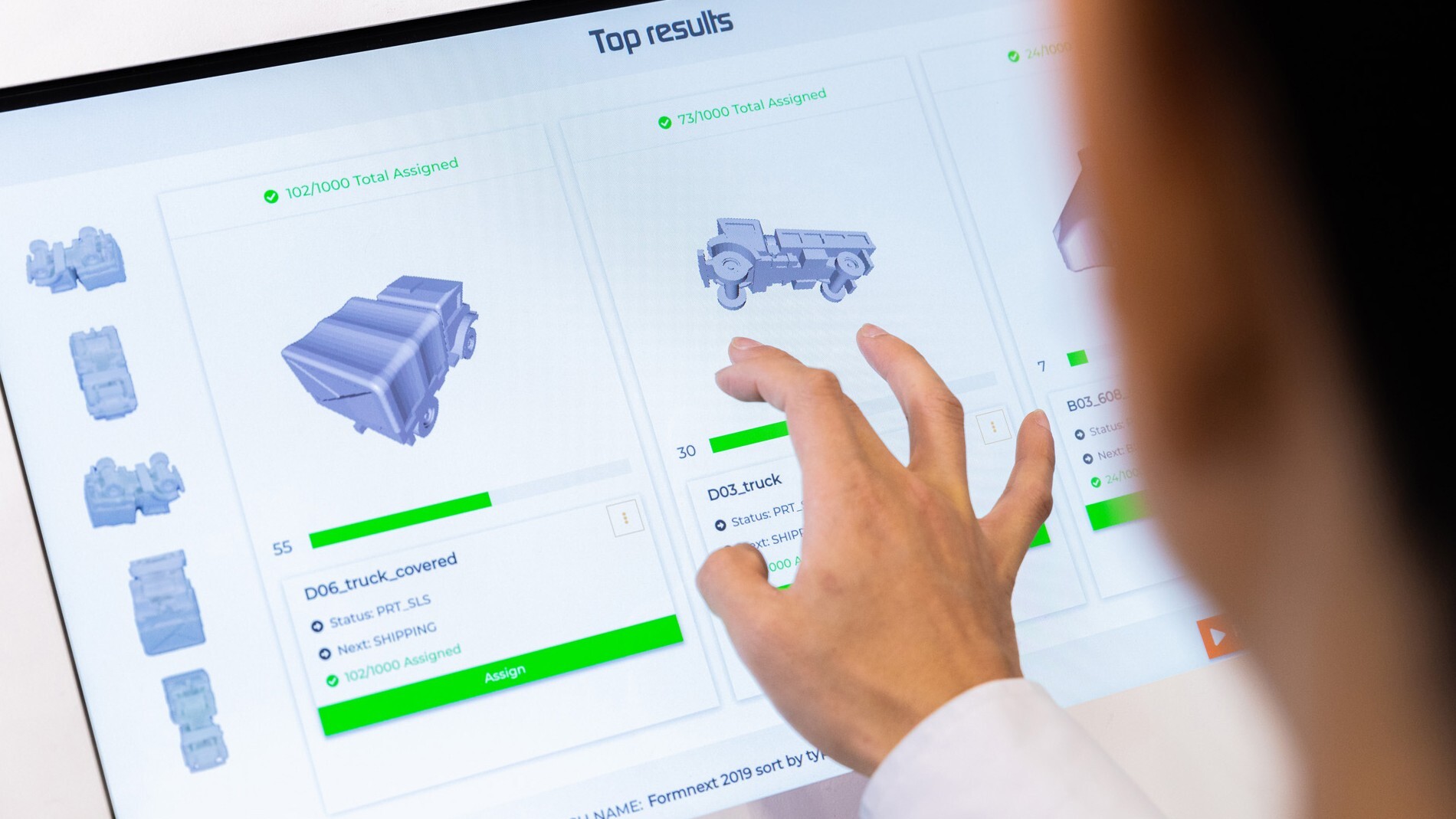
Problemstellung
Vor dem Sinterprozess werden alle relevanten Projektdaten in das LMD ERP-System von Freiblick eingepflegt. Dazu gehören Auftragserfassung, Arbeitsplanung, Kundendaten, Ansprechpartner, Projektnummern, Projektaufgaben und Zielsetzungen. Dieser Workflow stellt sicher, dass alle Anforderungen und To-Dos, die mit dem Kunden vereinbart wurden, lückenlos erfasst sind.
Nach der Arbeitsplanung werden die Bauteile für den Produktionsprozess zusammengefasst, gepackt und wirtschaftlich verschachtelt. Ziel ist es, die Maschinenkapazitäten der additiven Fertigung maximal auszunutzen. Die Auswahl der passenden Maschinen erfolgt anhand von Material, Lieferzeit und spezifischen Ansprüchen. Der Prozess des Packens erfolgt vollautomatisch.
Nach der Fertigung werden die Bauteile ausgepackt, vorgereinigt und gestrahlt. An diesem Punkt liegen sie jedoch ungeordnet vor, und die zuvor gepflegte Ordnung aus der Datenbank geht verloren. Jedes Bauteil muss nun wieder seinem ursprünglichen Projekt zugeordnet werden – ein zeitaufwändiges und fehleranfälliges Verfahren.

Ist-Zustand
Momentan erfolgt die Zuordnung der Bauteile manuell. Mitarbeiter nutzen Bilder aus der Datenbank, um die Bauteile anhand ihres Erscheinungsbilds zu identifizieren. Da die Bauteile meist keine Kennzeichnung tragen, ist der Prozess komplex und fehleranfällig. Begleitdokumente und Kistenaufkleber werden ausgedruckt und den Mitarbeitern bereitgestellt. Das manuelle Sortieren verursacht hohen Aufwand, Fehler, Stress und Papierverbrauch.
Zusätzlich prüfen die Mitarbeiter die Bauteile auf Qualitätsmängel wie Kratzer, Risse oder Maßabweichungen und dokumentieren diese Ergebnisse. Die Ursachen von Fertigungsfehlern werden jedoch häufig nicht ausreichend untersucht, was zu Folgefehlern und schlechter Kommunikation führt. Fehlende oder mangelhafte Dokumentation erhöht das Risiko, fehlerhafte Teile an Kunden zu liefern, was zu Reklamationen, Lieferverzug und langfristigen Problemen führt.
Lösung
Die Implementierung einer automatisierten Anlage von LMD/AM Flow reduziert die genannten Probleme erheblich. Die Kernaufgabe der Anlage besteht darin, Bauteile vollautomatisch zu erkennen, zu vermessen und zu dokumentieren – sekundenschnell und ohne bauteilspezifische Programmierung.
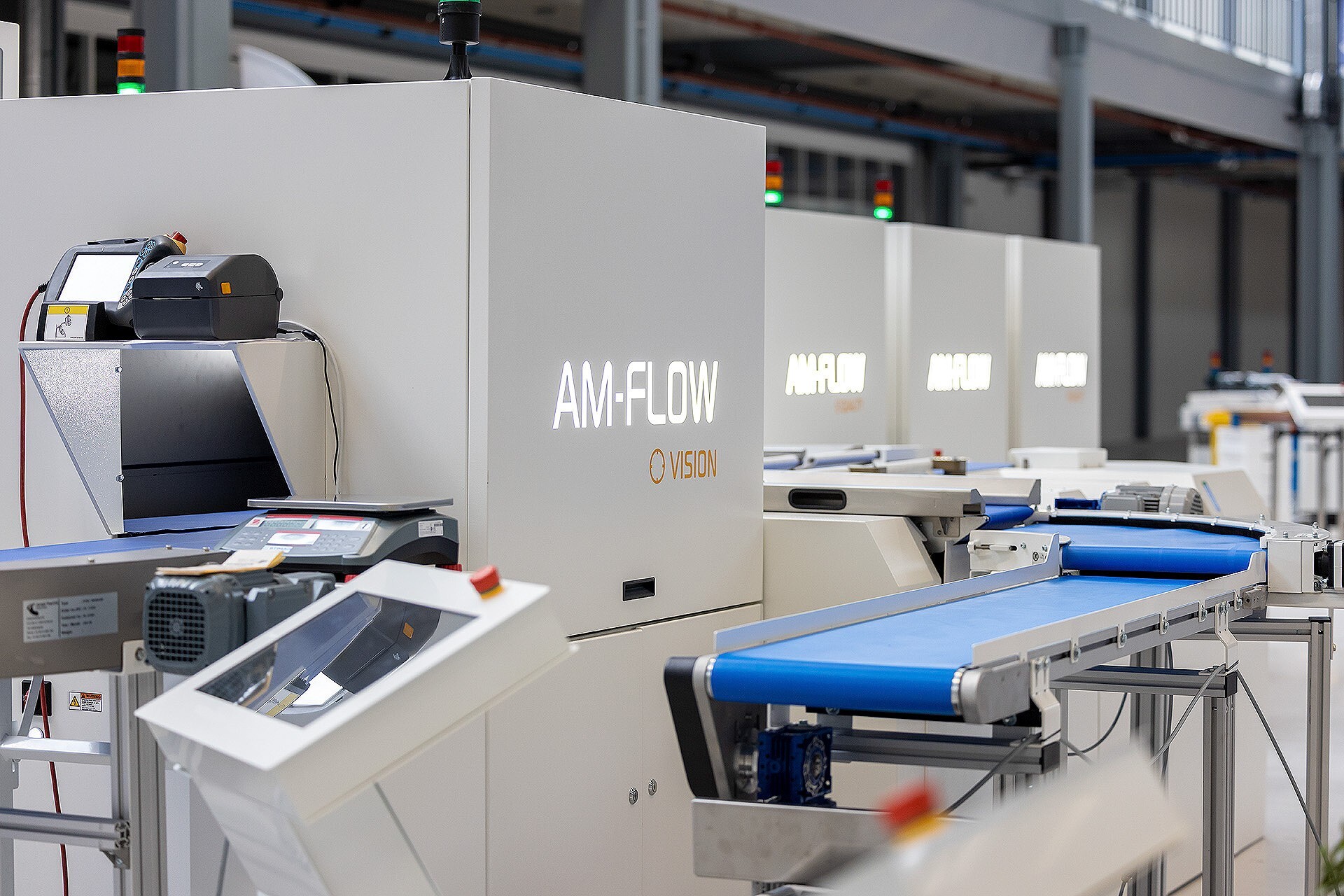
Funktionsweise der Anlage:
- Erkennung und Zuordnung:
- 180°-Erkennung über mehrere Kameras.
- Abgleich mit ERP-Daten zur Projektzugehörigkeit.
- Vermessung und Qualitätskontrolle:
- Erstellung einer Punktewolke per Scanner.
- Abgleich mit virtuellen STL-Daten zur Ermittlung von Abweichungen.
- Farb- und Oberflächenerkennung.
- Dokumentation:
- Automatische Protokollierung von Differenzen.
- Erkennung und Sperrung von Ausschussteilen.
- Bereitstellung digitaler Daten für Folgearbeiten.
- Optimierung der Kommunikation:
- Digitale Bereitstellung aller relevanten Informationen bis hin zur Werkbank.
- Keine Notwendigkeit für gedruckte Dokumente.
Zukunftsausblick

In weiteren Ausbaustufen sollen Roboter die Bauteile automatisch in die entsprechenden Projektkisten sortieren – ebenfalls ohne aufwendiges Anlernen. Damit wird der gesamte Prozess noch effizienter, fehlerfreier und kostengünstiger.
Durch diese Lösung entsteht eine klare Struktur und Ordnung, die es ermöglicht, Folgearbeiten reibungslos zu planen und durchzuführen. Der Einsatz moderner Technologie minimiert menschliche Fehler und sorgt für eine hohe Produktqualität und Kundenzufriedenheit.